One of the most exciting things about working on pianos and other keyboard instruments such as harpsichords and celestas is the sheer variety of problems one must solve. Many problems qualify as “standard” problems which occur often and can be solved in a similar manner for every instrument. However there are also many unusual problems which cannot be found in any textbook and require a special degree of detective work to fix.
A client in 2024 contacted me because several keys in the top octave were staying depressed. When I arrive and inspected the piano I could see the problem which he described, but determining the cause was another matter.
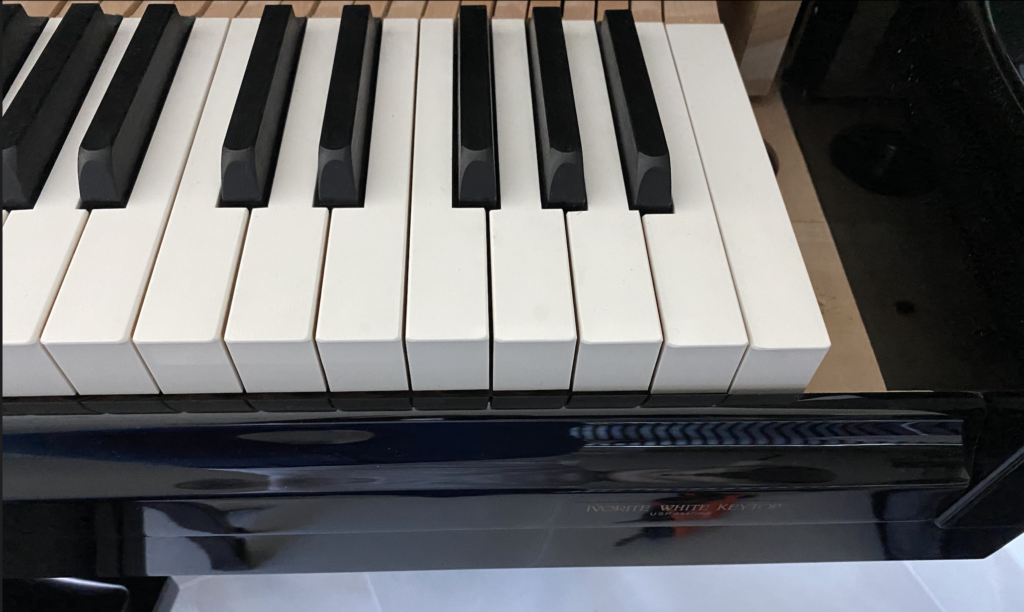
When I looked inside I could see that the hammers were elevated as well.
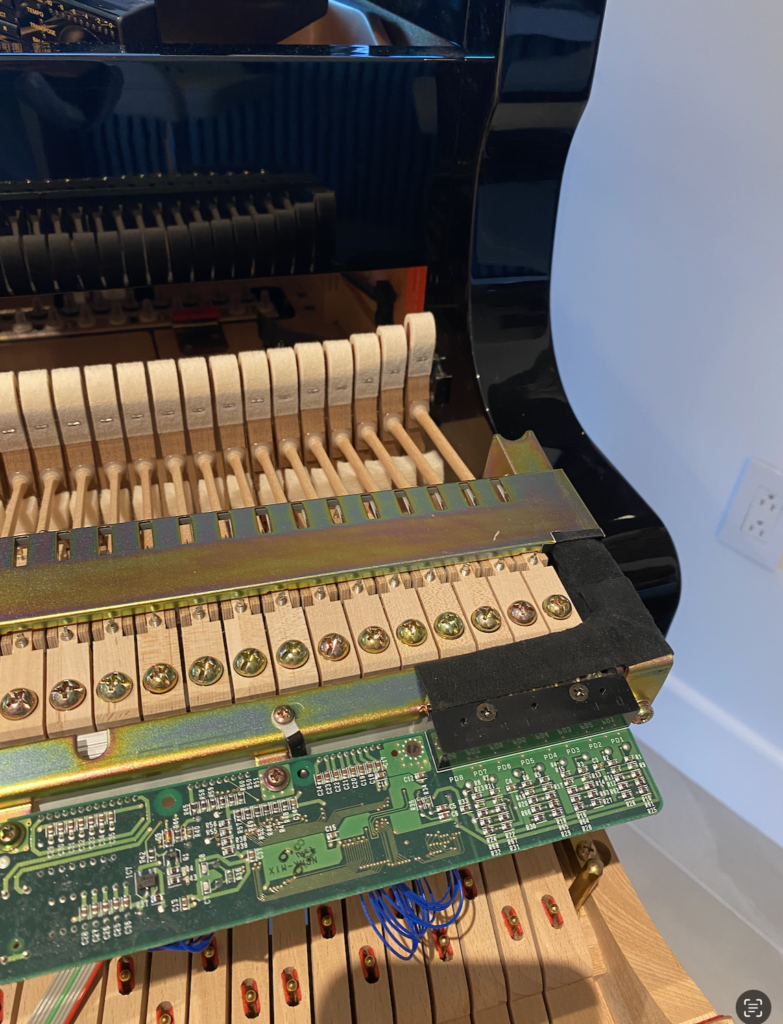
I checked all the usual issues such as a foreign object, regulation settings, friction, etc. I checked if perhaps the player piano mechanism was the cause by resetting it. I took the whole piano apart and could find nothing out of the ordinary. At these times I often remind myself “Pianos must obey the laws of Newtonian physics.” meaning that even when it seems like there is a ghost in the machine everything must have a logical explanation. A key is a simple lever and if it is depressed something must be applying force to it.
I contacted several other technicians including the manufacturer to get their thoughts. Everyone was stumped. Finally one of my trusted colleagues Nick Morris who specializes in player pianos mentioned a situation he experienced years before in which movers had screwed the leg bolts in too far and they interfered with the keys. I recalled the client had moved the piano recently. I called the client and asked him if there was any problem with the leg bolts. He said the movers had lost the bolts and it took them a long time to find replacements. This sounded like a strong theory.
I inspected the interior of the piano again and saw that the leg bolts were indeed protruding inside the piano. Now I had a smoking gun.
What had happened in this case is that the movers lost the bolts, ordered the wrong bolts, then used high powered tools to force them which stripped the threads. Never hire regular movers to move your piano. Here you can see a comparison of the correct bolt which is the shorter one vs. the incorrect bolt which is the longer one. Notice the movers added five washers to try to make the longer bolt work.
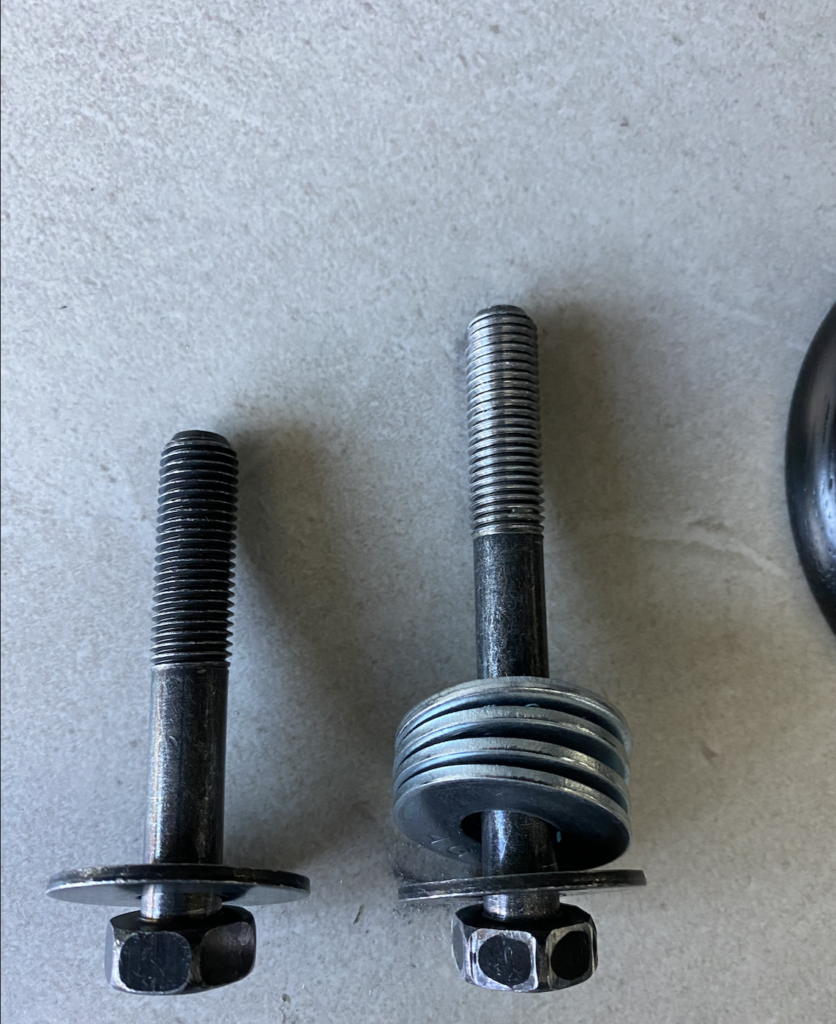
Now the hard part began – removing the bolts. Normally removing leg bolts is easy and can be accomplished with modest tools. I tried with my normal wrench and found that the bolts would not budge. Therefore I aquired a “cheater bar” which was nothing more than a 36″ metal pipe. This tripled my leverage.
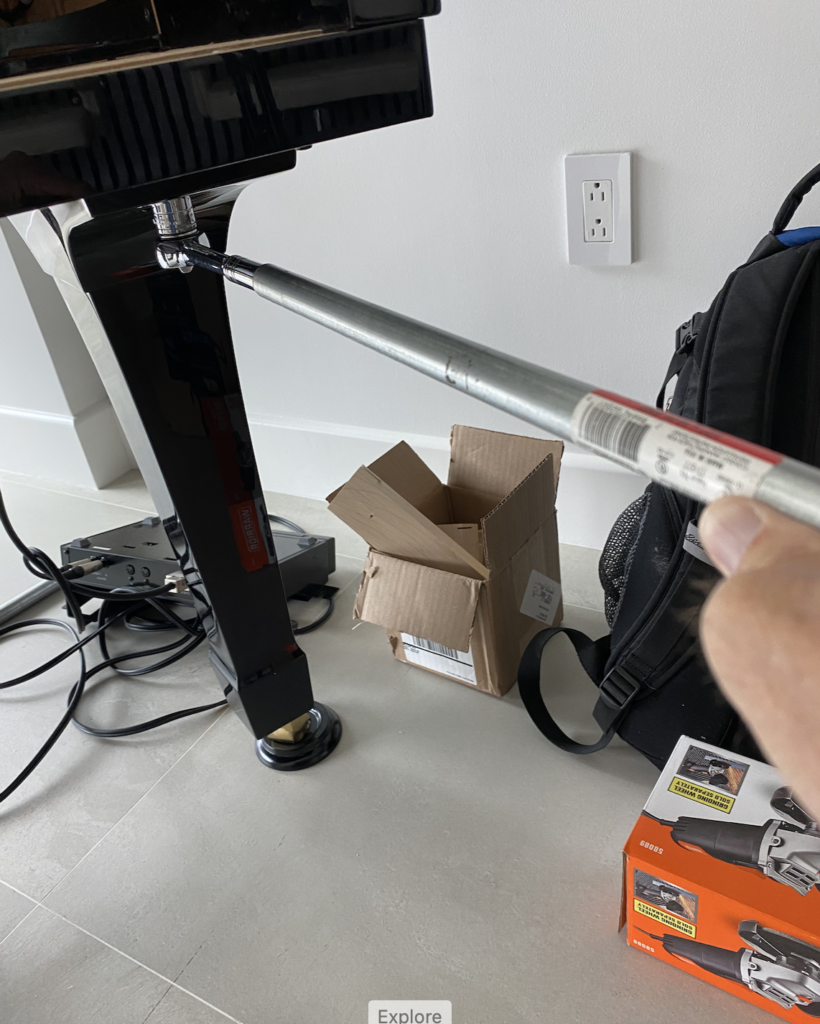
Even with this added leverage the work was grueling. Every turn took all of my strength. What should have taken minutes took hours. When I got to the last bolt, which was the most difficult of all, the bolt was so resistant to turn that it tore the screws out of the plate.
The threaded female metal plate that the bolt was supposed to screw into was totally detached. Now I had a much more serious problem. In the video below you can see that the bolt and the plate are married together but totally detached from the wood inside the piano.
The only way to remove the leg bolt from the female plate would be to secure the plate somehow so that it would not turn. However you can imagine that with 36″ of leverage the amount of torque being applied was substantial so stabilizing it would be next to impossible. I tried many strategies including vice grips, clamps, even fashioning custom tools in my shop. All of them failed.
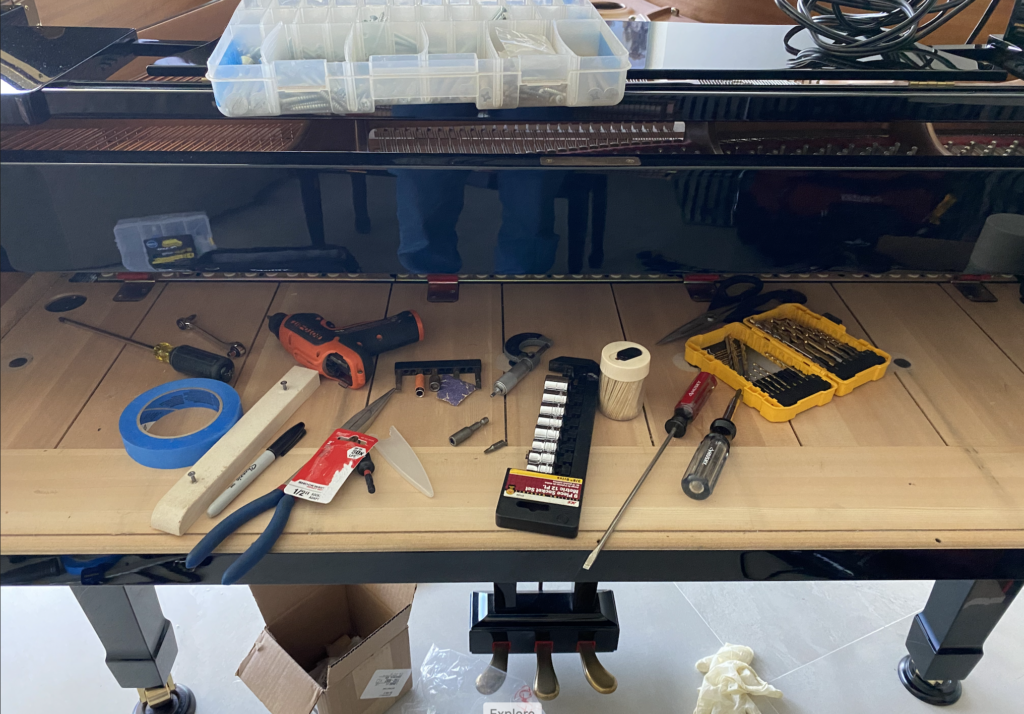
Now it was time to go to the last resort which was cutting through the steel bolt and replacing the bolt and the plate entirely. I acquired a tool known as an “angle grinder” which is capable of cutting even the hardest steel. I tested it in my workshop to make sure it would work.
Not wanting to take any chances I also acquired another tool recommended by my expert woodworking friend Kurt Gary called a “Pin Wrench”. This is a tool designed to hold the plate stationary while I turn the bolt.
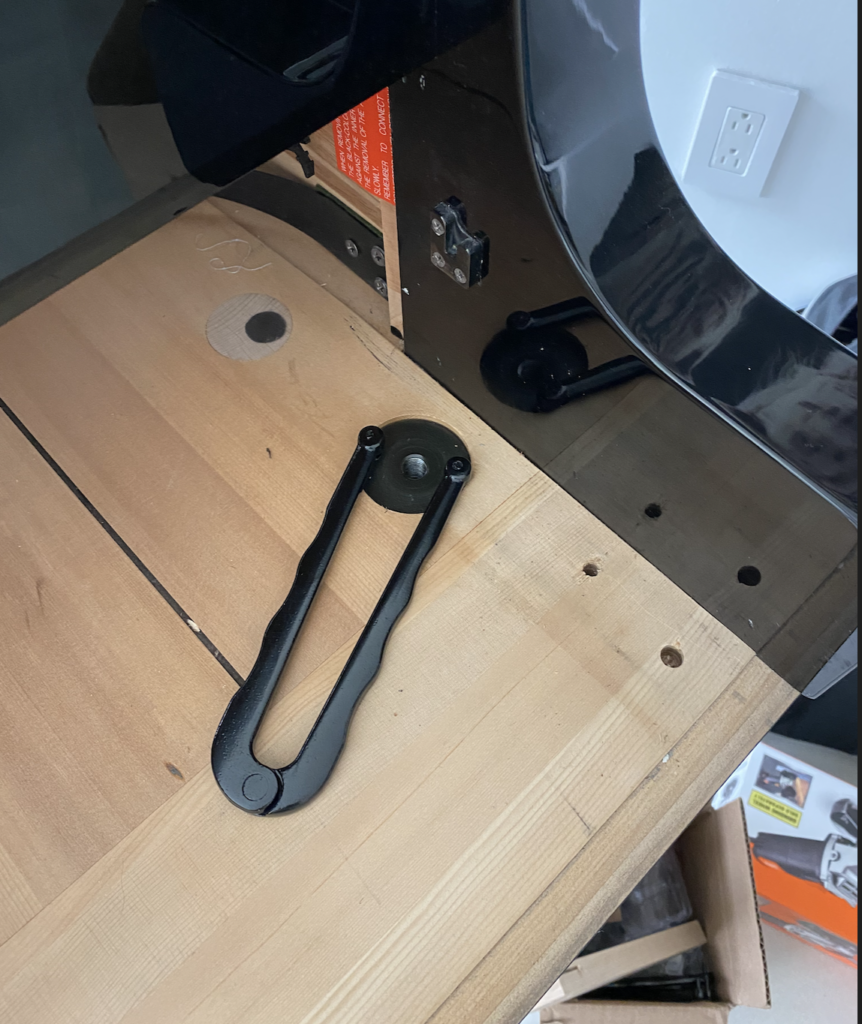
I arrived ready for anything but prepared to cut the bolt in half if needed. By a miracle the pin wrench worked and I got the last bolt out!
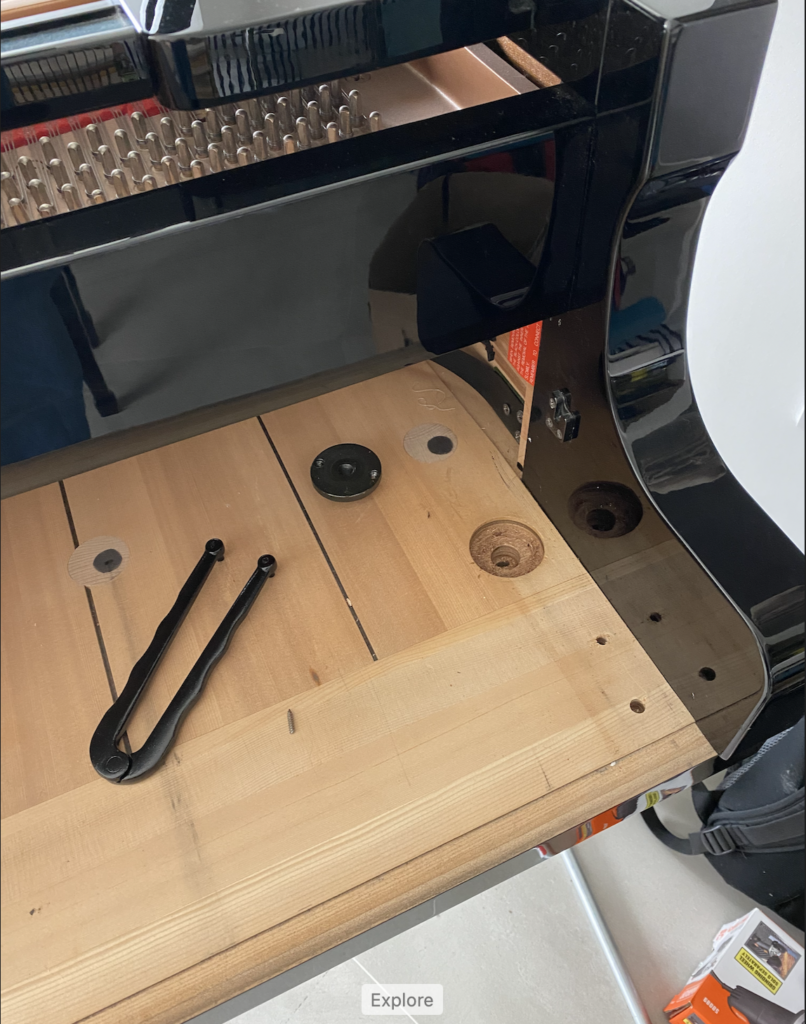
I repaired the damaged wood, installed a new plate, a new bolt and the piano was now fully functional.
There were several takeaways from this Herculean adventure. First, never use regular movers to move your piano. I wish I could say this story was unique but I get calls like this all the time from customers who’s pianos were damaged by movers. This customer was actually lucky because the problem was solvable. Often it is not.
Next, knowledge is one thing but in truly difficult situations creativity and tenacity are what’s needed.
If you would like to schedule an appointment to get your piano tuned, please contact L.A. Piano Tuning by clicking the link below: